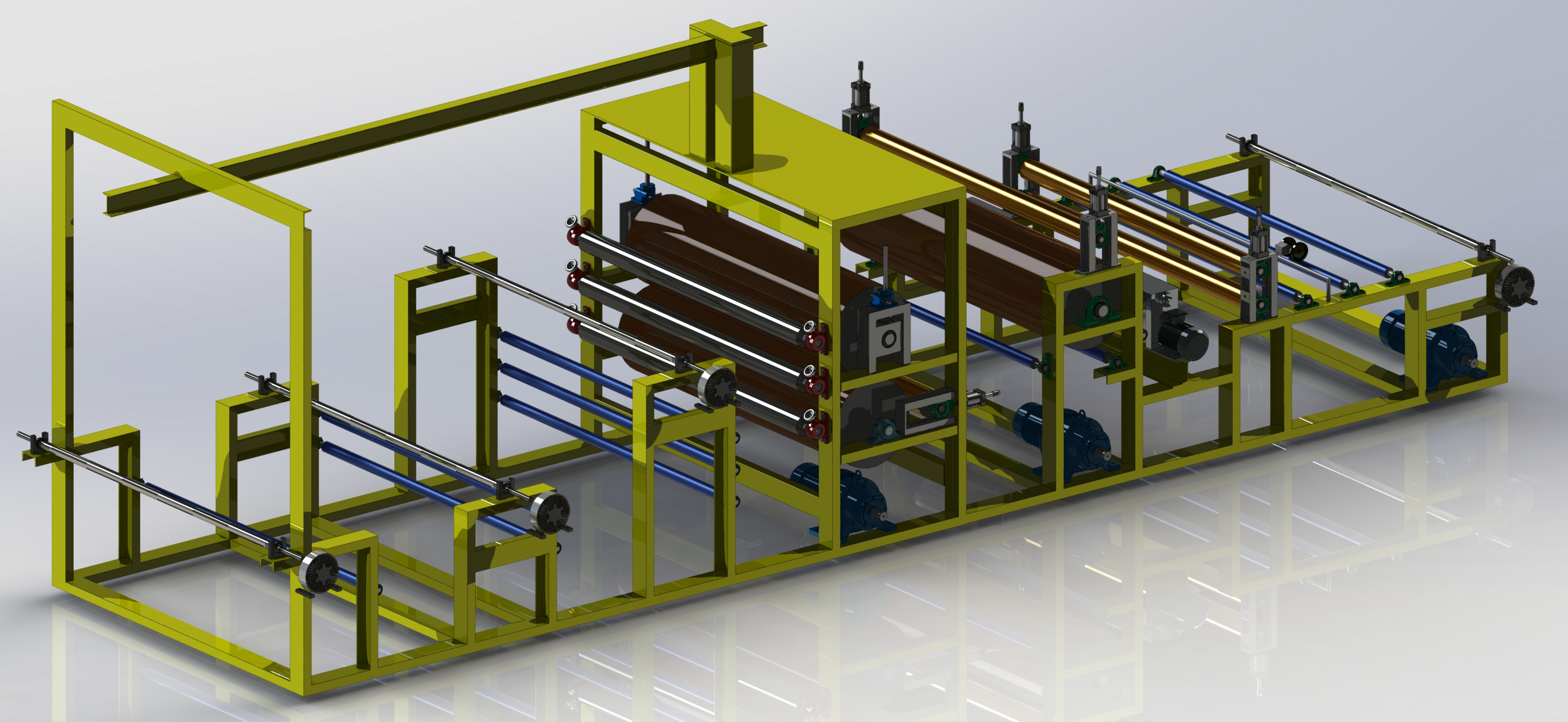
Operational precautions:
The operator can operate the device only after he is fully familiar with the performance of the Heat Press Lamination Machine and the working principle. This equipment must be operated by a dedicated person, and non-operators should not open and move.
Before production, check whether the electrical appliances such as cables, circuit breakers, contactors, and motors meet the requirements.
Before production, check whether the three-phase power supply is balanced. It is strictly forbidden to start the equipment in phase loss.
During the production period, it is necessary to check whether the rotary joints are safe, whether the pipelines are unblocked, whether there is any damage, oil leakage, and timely elimination.
Before production, check whether the pressure of each barometer is normal, whether there is air leakage in the gas path, and repair it in time.
Check the tightening of each joint before production, whether there is looseness or shedding, and repair it in time.
Before the equipment is mass-produced, a small amount of test should be done first, and then it can be mass-produced after success.
Before production, the lubrication conditions of each hydraulic station, reducer, bearing shoe box and lead screw should be checked. Hydraulic oil and lubricating oil should be added correctly and timely.
After the Heat Press Lamination Machine is stopped, it is necessary to pick up the dust-collecting parts and other accessories in time, and apply the rubber roller to remove the residual materials and dirt from the machine for the next use.
It is forbidden to contact the corrosive liquid with the rubber roller, and ensure that the surface of each drive roller is clean and free of foreign matter.
It is forbidden to stack debris around the host system, and keep the surrounding area clean and free of foreign matter. Guaranteed a certain heat dissipation effect.
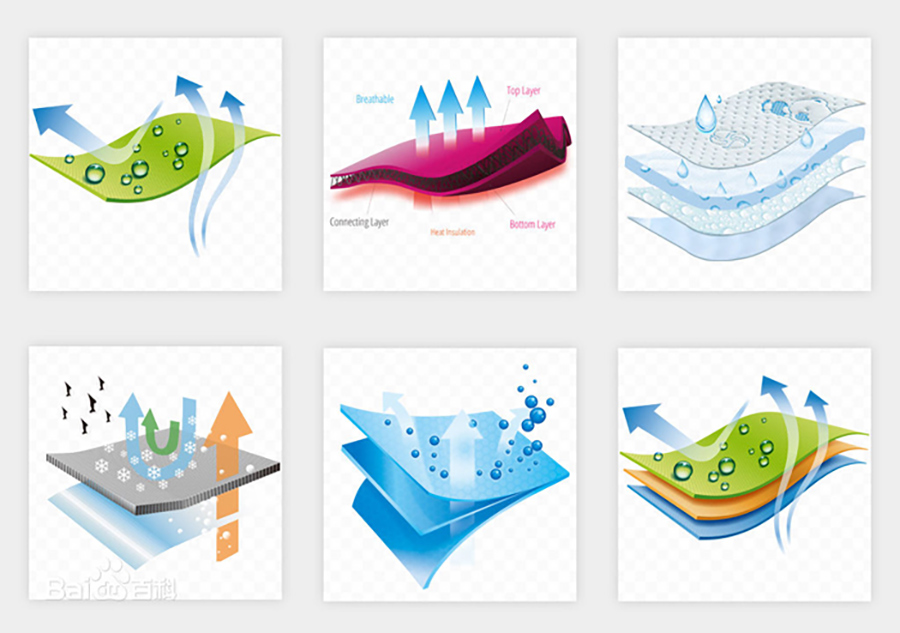
Maintenance
The gear unit should be replaced once every six months of use.
The dust collection device is regularly inspected and replaced according to actual production conditions.
The N46 or N32 anti-wear hydraulic oil should be replaced once every six months for the hydraulic tank.
Check the hydraulic tank and the hot oil tank once a month to remove grease, remove impurities, and add lubricant and heat transfer oil.
Bearings, screws are filled with oil every shift.
After each stop, the accessories such as dust collection parts and anilox roller must be removed in time to remove residual materials and dirt from all parts of the Heat Press Lamination Machine.
The chain is checked every shift to ensure normal lubrication and timely tension.
Check the connecting parts every shift, whether the fasteners are loose or missing, and tighten them in time.
Check the oil pump, cylinder, solenoid valve, distribution valve, oil pipe and other joints for oil leakage every shift.
Post time: Dec-14-2023